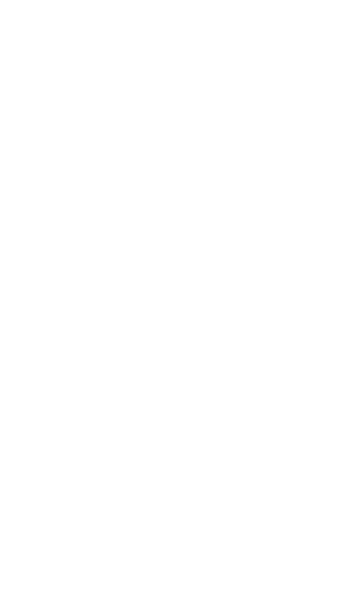
High-temperature air preheater
Air preheater (APH) is widely used in the production process of carbon black, and it is one of the most important production equipment. At the same time, APHs have also been promoted to other industries. At present, they have gradually been used in high-energy-consuming industries such as coal gas. It is gradually replacing traditional low temperature and low efficiency heat exchanger. APH improves the heat recovery rate of coal gas, optimizes the coal-to-gas production process, enables all grades of coal to be used as raw materials. By using the high-temperature APH, it could reduce production costs, brings considerable economic benefits to customers, and brings good Social benefits as well. The high-temperature air preheater, which is designed and produced by Doright for coal-to-gas usage, utilize the thermal energy released during the process of cooling the high temperature (920 °C) gas to 680 °C to heat the air (25 °C) to 600 °C, which will be used for supporting reaction or combustion. Compared with 300 °C air, 600 °C air participates in combustion, the output can be increased by 45%, while saving fuel by 9.3% -13.2%.
High-temperature air preheater is the most important energy-saving equipment in carbon black production line. It can preheat the process air to 650 °C - 950 °C. By increasing the air outlet temperature, it is conducive to increasing the carbon black yield and strengthening the carbon black reaction conditions, increasing the heat value of the exhaust gas, and more beneficial to the comprehensive utilization of the exhaust gas.
Product structure
The design of the air preheater is that the heat exchange tube bundle is installed inside the shell. The carbon black flue gas circulates from the inside of the heat exchange tube, while the air is outside the heat exchange tube. The air is deflected by the baffle plates to exchange heat with the carbon black flue gas. The high-temperature end of the heat exchange tube is connected to the two bottom tube sheets through sleeve tubes, and the upper part of the heat exchange tube is connected to the top tube sheet using a single tube compensator (or sealing device). It solves the differential expansion problem between the shell and the heat exchange tube during operation.
Air preheater type
Sliding type design
The sealing structure of the heat exchange tube and the tube sheet is freely sliding through the sealing device, which can make the tube work under stress-free condition, avoiding uneven expansion due to the heating of the tube bundle.
Tube compensator type design
Every heat exchange tube has an individual tube compensator, which could solve the problem of uneven thermal expansion between different heat exchange tubes during operation.
Air preheaters are also widely used in energy recovery processes in other industries, such as steel, glass furnaces, waste incineration, sludge incineration, power plants and coal chemical industries.